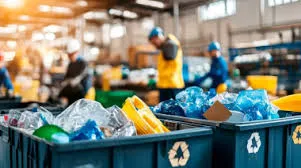
Presentan un proyecto innovador para transformar el reciclaje en Argentina
Un proyecto desarrollado por Dow, empresa con plantas productivas de polietileno en la región, marcaría un punto de inflexión en la industria del reciclaje y la gestión de residuos en Argentina